
My printing crew hardly misses a beat and we don’t miss the deadline. No matter the age, or oddball part, the parts department makes sure I’ll have what I need the next morning. An instrumental partner in our success.Ī frantic call in the middle of the night is always met on the other end of the line by an experienced member of their service staff who expertly diagnoses my issue, and starts the process of solving our problem. They are part of the fabric that is Ink Brigade.
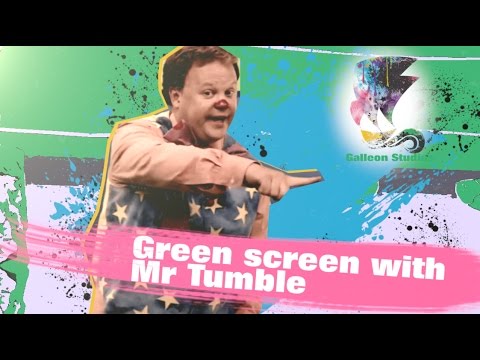
Even years after the sale, we can count on M&R 24/7. It’s times like those that we’re glad we chose M&R as our equipment manufacturer. Even with that said, parts get old and can wear out.

M&R makes the most high quality screen printing equipment in the world. Simply put, the Gauntlet III is a beast and is built to run 24/7/365. We are able to run as fast as we can clear a screen and dry our underbase. Overall, we have seen an increase in our production numbers due to the efficiencies gained with the newest technology on the market. We have not had any problems to date with the machine but are at ease knowing that all parts that we could ever need are able to be overnighted to us. Having a built-in maintenance schedule for the machine is another perk and allows management to easily assure that the presses are being properly maintained. The touchscreen interface is very user friendly and easy to make adjustments when needed. The addition of the laser for print placements has saved us valuable time where we used to mark our pallets with a T-Square. We were able to run the machine comfortably at 920 pieces per hour. Our first job was a 9-color on dark apparel with a 17” print stroke and one flash.
#MR SCREENIE PLUS#
It is also a plus to be able to adjust in 1/16” increments when needed. We have found that the individual off-contact for each printhead helps with various printing techniques. We have already put over 120,000 impressions on the machine and it is still going strong. We have had our Gauntlet III in production for nearly 3 months and have been thrilled with the machine. Low operating costs, versatile design features, and competitive pricing make Eco-Tex the ideal addition to any screen printing operation. Stainless-steel construction minimizes maintenance and ensures a long, productive life. The machine’s compact footprint makes it easy to place in most shops, and its reversible conveyor allows right-to-left, left-to-right or return-to-entry-point movement, expanding options for machine placement. Eco-Tex offers user-friendly touchscreen control over all operations, and it includes complete self-diagnostic functionality. Eco-Tex is economical to operate, and it helps shops keep screen-cleaning/reclaiming areas clean. Screen holders are available in numerous sizes, and additional holders can be purchased for added convenience and faster turnaround.

#MR SCREENIE FREE#
In addition, the operator is free to perform other tasks while the screens are being cleaned, increasing productivity. Since it only requires a single operator, Eco-Tex reduces per-screen labor costs. Eco-Tex has no external moving parts, and it eliminates direct employee exposure to the cleaning process. The easy-to-clean filtration system helps prevent foreign matter from contaminating cleaning chemicals and jet nozzles. A dual-chamber Eco-Tex can nearly double that figure. A single-chamber Eco-Tex can typically clean up to 160 screens per shift (based on two screens per cycle). Eco-Tex is modular, so an additional chamber can be added to increase production capacity. Cleaning solvents drain back into the holding tank after each cleaning cycle, reducing chemical use and lowering the cost of operation. An electric conveyor with stainless-steel rollers moves dirty screens into the chamber and clean screens out. The entire procedure takes place in a single automated cycle-and in a single chamber. Power-washing both sides of the screen simultaneously helps maintain screen mesh tension. Once the screens have been cleaned, Eco-Tex rinses them with a high-pressure fresh-water power wash. In the process, Eco-Tex reduces environmental impact and lowers operating costs by recirculating screen-cleaning chemicals. M&R’s Eco-Tex™ automates and simplifies the entire screen-cleaning process, and it handles screen frames up to 132 x 97 cm (52” x 38”).
